エンジニアレス…。
この言葉は我々が次世代の生産現場に提唱する何気ない言葉になりますが、これからは身近で当たり前のように聞くスタンダードな言葉になると考えています。
さて、サムネイル画像にある黒い物体は当社自信の新商品
その名も「EL-AT」/ エンジニアレスアタッチメント。今回はコチラを紹介していきたいと思います。
我々はいわゆる生産工場に纏わるお仕事をさせていただいておりますが、その中で今や見るのが珍しい事ではなくなった協働ロボットは業種問わず各生産現場に数多く導入されているのはご存じの通りかと思います。人と一緒に、または人の代わりにと何かと便利なロボットですが、実はこの子達が動くまでのプロセスと、動いた後のフォローが意外と大変なのは経験してみてわかること。
結果「あぁ、面倒くさい」と次回の導入に足踏みしてしまうこともありますよね?
しかし、協働ロボットが必要不可欠であるこの時代に見て見ぬふりは出来ず。。。そこで、もっと身近にそして簡単に導入のお手伝いが出来ればと思い開発したのがコチラの商品「EL-AT」です。
” エンジニアに頼らずあらゆる生産現場に可能性を ”
従来はロボットハンドの設計、別品種へのユニット交換作業、そしてロボットプログラムの変更など
現場とエンジニアは常におんぶにだっこの状態で生産をしてきましたが、今後は手をつなぐ程度で良いのではないかと考える本商品は、各メーカーで専用ベースを設け、ロボット側 / チャック側のそれぞれにラインナップがありシンプルな構造のため専任者での交換作業が必要なく、用途 / 生産に合わせた段取り替えがスムーズに行えることと各種専用設計となっているため、” 設計 ” をする必要がなく ” 選択 ” のみで解決することで設計時間の短縮やエンジニア以外の方でも導入可能な ” エンジニアレス “ を可能にしたアタッチメントになります。また、協働ロボットを使用するにあたってどうしてもネックとなる可搬重量にも着目している魅力的な商品です。
「簡単 ✖ コスパ」「軽さ ✖ 安全」この2✖2本柱を軸に豊富なラインナップをご用意しておりますので
詳細は専用ページにてご覧ください。 https://aswitch.co.jp/?page_id=495
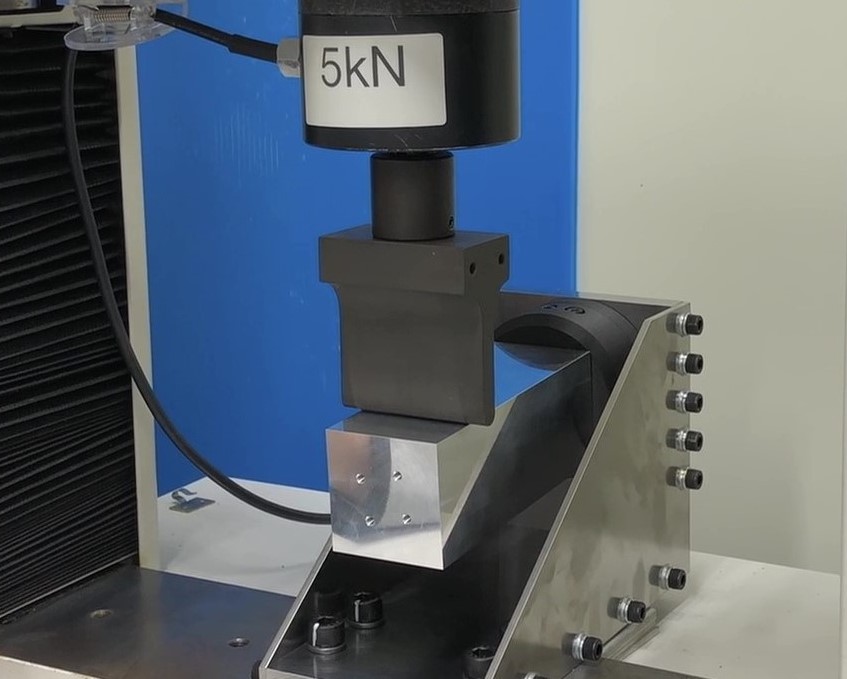
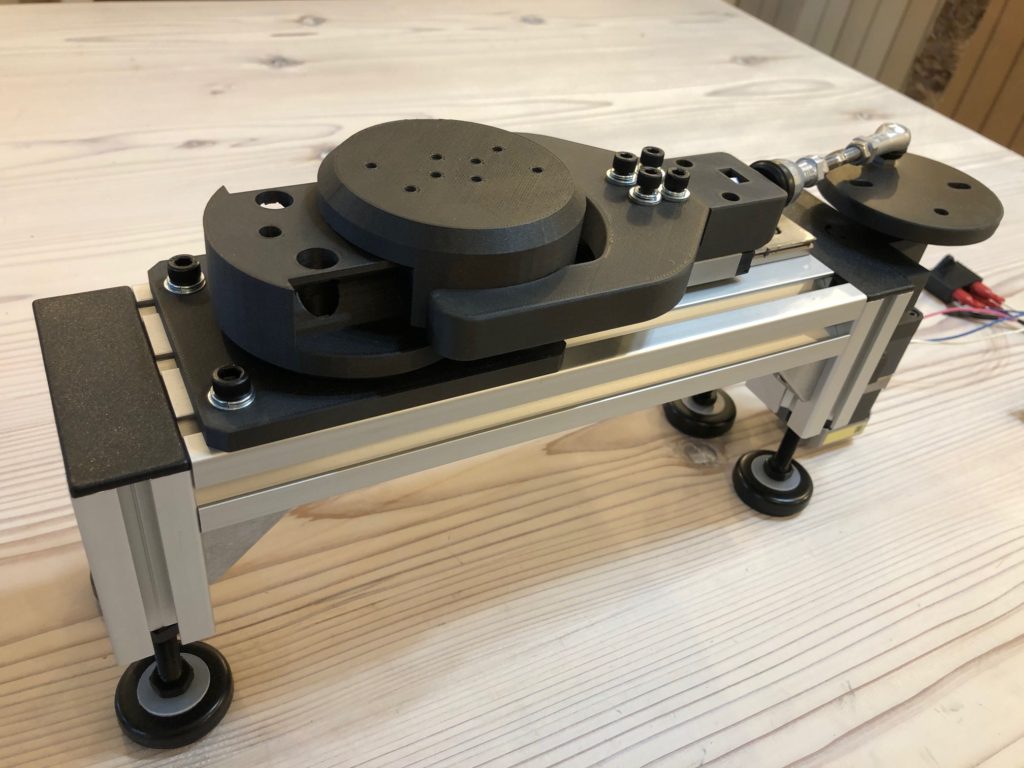
もちろん検査機関での耐久テストを行い、考えられる負荷条件を四方から確認の上、安全性を追求。
また自社製の治具でひたすら摺動テストを行い消耗度も確認しています。
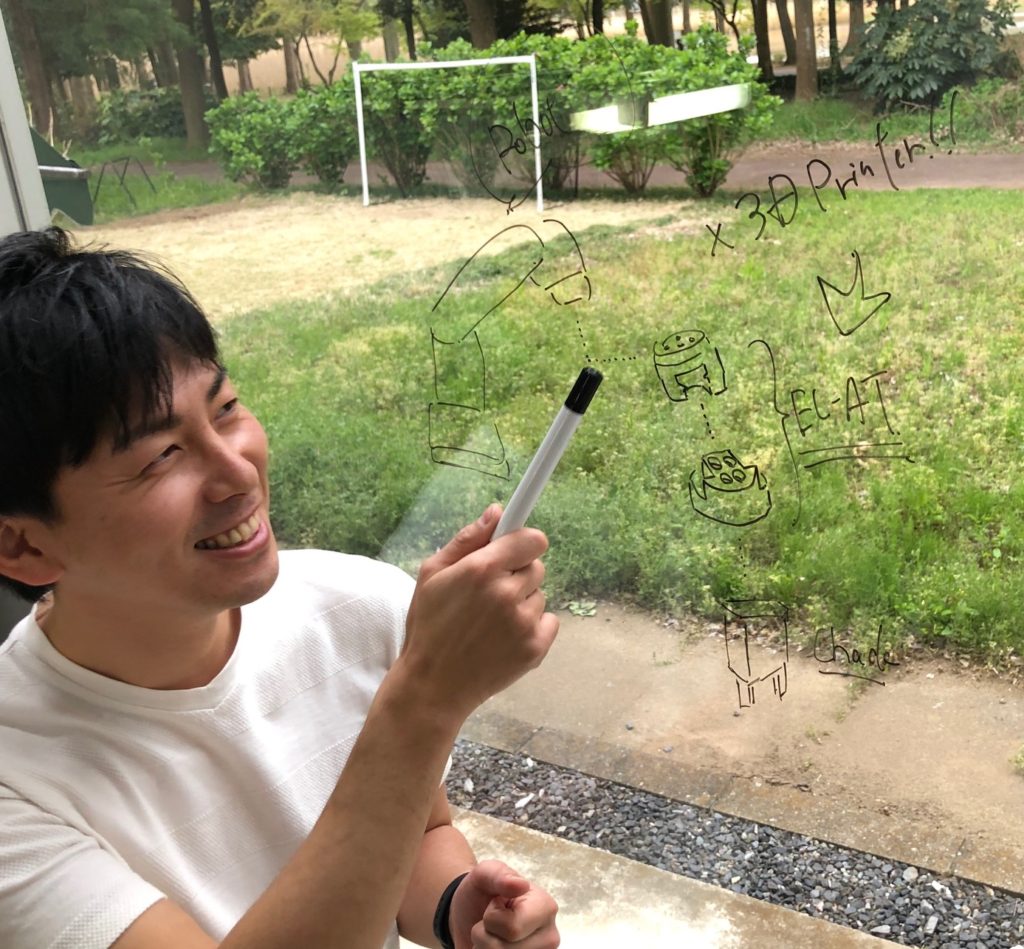
今回は当社の技術責任者であり「EL-AT」の開発者でもある門(カド)さんに話を聞いてみました。
(記者 T)「なぜこの商品を開発しようと思ったのですか?」
(門さん)「んー、こんなのあったらいいなーって思ったので作ってみました。
だって、協働ロボットを使用した設備を設計する上で一番悩むところなんだもん」
との事。
彼はこの道十数年と業界に精通している上に、彼自身が設計者であり、只々簡単を求めていたのだと思います。
(記者 T)「アピールポイントはありますか?」
(門さん)「うん、まずね、設計と現場が気兼ねなく使えるってところ!それとコイツは可能性を秘
めてるからね!」
(記者 T)「・・・」
(門さん) 「えっとー、コイツは2つの視点を持ちながら、エンジニアの負荷軽減と現場の視野を広
げてくれる…。
1つ目はエンジニアの視点から考えたときに、すでに市場に出ているモノは値段も高く
汎用性も強すぎるため、一見設計が楽になりそうに思うが、選定~採用までにどうして
も時間や労力を費やしてしまう。 実はこの選定という作業自体が、汎用性を高めすぎ
たことによって、設計者の負担になってると思うんだよね。
2つ目は現場作業者の視点から考えたとき、精密で高価なモノって取り扱いにくいとい
う拒否感が生まれません?現場で作業者にヒアリングすると、従来のモノは機能面を配
慮していることから部品点数も多いため、いざメンテナンスをしようとした時、何かと
エンジニアが対応しないといけないってよく聞くんだよね。
これらの問題を解消するために、専用設計と構造のシンプル化が外せないキーワードだ
ったんだ。そして、3Dプリンターで製作することで新しい可能性を取り入れたことも
一押しのポイントかな」
どうやら設計には設計の、また現場には現場の苦労が多いにあるようです。
これが実の声です。
やれAIだのIoTだのとはいっても、実状はまだまだ現場主義であり大事なのはやはり現場。
なかなか表立って出てこない生産現場には必ず人が介在することを忘れてはいけません。
私たちは、今の時代に合った「速さ」を求めながら
より現場目線での「アナログフィールドの速さ」も追求しています。
So Speedy…